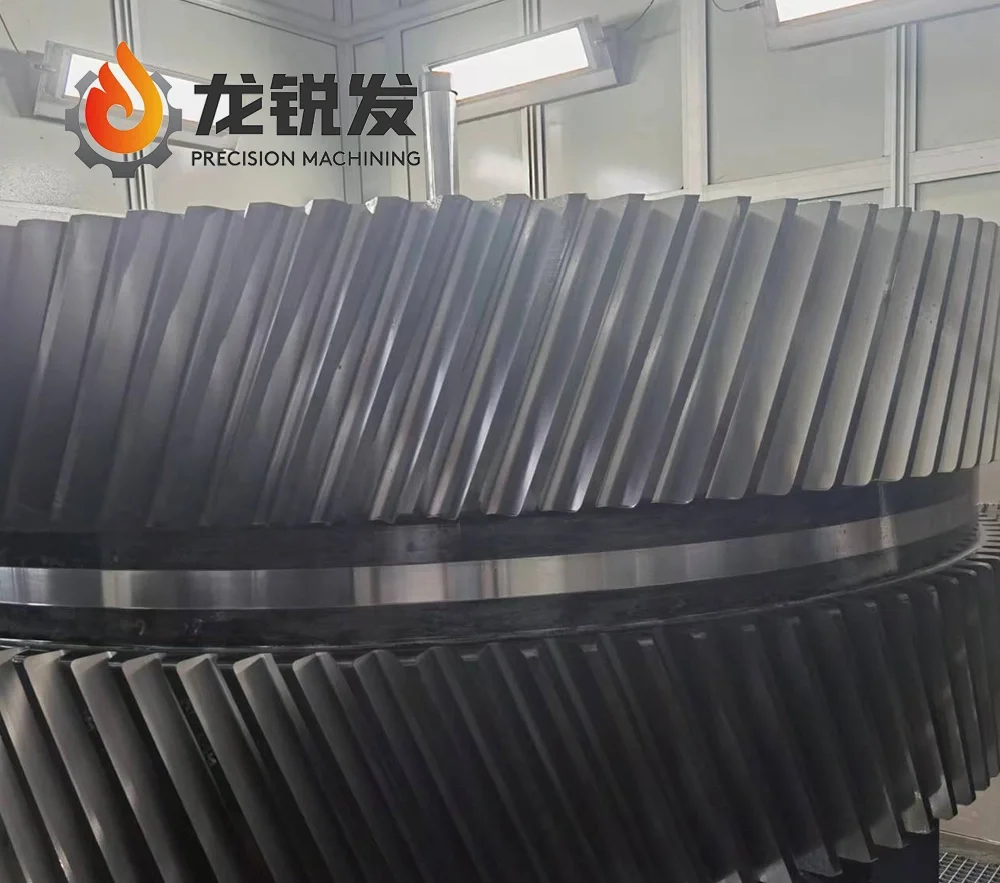
In the world of industrial machinery, gear manufacturing plays a crucial role in ensuring smooth and efficient mechanical operations. Among the many types of gears available, herringbone gears stand out for their exceptional strength, durability, and ability to handle heavy loads with minimal noise and vibration. In this blog post, Longruifa will explore the intricacies of high precision industrial herringbone gear manufacturing, highlighting the processes, benefits, and applications of these remarkable mechanical components.
What is High Precision Industrial Herringbone Gear for sale?
Herringbone gears are a type of double helical gear characterized by a V-shaped tooth design. Unlike standard helical gears, which have a single helix angle, herringbone gears feature opposing helix angles that meet at a central point, forming a herringbone-like pattern. This unique design eliminates axial thrust, making them ideal for high-load applications in industries such as aerospace, marine, automotive, and heavy machinery.
Importance of High Precision in Herringbone Gear Manufacturing
Precision is a critical factor in herringbone gear manufacturing, as even the smallest deviations in tooth geometry can lead to performance issues such as increased noise, inefficiency, and premature wear. High precision industrial herringbone gear manufacturing ensures that gears meet exacting tolerances, allowing for optimal power transmission, reduced friction, and extended service life.
High Precision Herringbone Gear Manufacturing Process
Manufacturing herringbone gears involves multiple stages, each requiring state-of-the-art technology and expert craftsmanship. Below are the essential steps in the process:
1. Material Selection
Choosing the right material is fundamental in gear manufacturing. Herringbone gears are typically made from high-strength materials such as:
- Alloy steels (e.g., 4140, 4340)
- Cast iron
- Bronze
- Case-hardened steel
- Nitriding steel
The choice of material depends on the intended application, required load capacity, and environmental conditions.
2. Gear Cutting
Once the material is selected, the gear cutting process begins. Several methods can be used to cut herringbone gears, including:
- Hobbing: A highly efficient method using a hob cutter to generate precise gear teeth.
- Shaping: Involves a pinion cutter to incrementally cut the teeth.
- Milling: Utilizes CNC machines to achieve tight tolerances and complex geometries.
- Broaching: Suitable for high-production runs and intricate profiles.
3. Heat Treatment
Heat treatment is essential for enhancing the strength, hardness, and wear resistance of herringbone gears. Common heat treatment processes include:
- Case Hardening: Adds a hard outer layer while maintaining a tough core.
- Induction Hardening: Improves surface hardness through localized heating.
- Nitriding: Enhances wear resistance without significant distortion.
4. Grinding and Finishing
To achieve high precision industrial herringbone gear manufacturing, grinding and finishing processes are crucial. Precision grinding removes any irregularities and ensures smooth operation. Lapping and honing further refine the gear teeth, reducing friction and noise levels.
5. Quality Inspection and Testing
No gear leaves the production facility without rigorous quality control. Inspection methods include:
- Coordinate Measuring Machines (CMMs) for precise dimensional checks.
- Gear Inspection Machines to verify tooth geometry and alignment.
- Non-Destructive Testing (NDT) such as ultrasonic or magnetic particle inspection to detect hidden defects.
- Load Testing to simulate real-world operating conditions and ensure durability.
Benefits of High Precision Herringbone Gear
Investing in precision manufacturing yields several advantages, including:
- Reduced Noise and Vibration: The opposing helix angles counteract axial thrust, leading to smoother operation.
- Enhanced Load Capacity: These gears can handle high torque and heavy loads efficiently.
- Longer Lifespan: High-quality materials and precision machining increase durability and reliability.
- Higher Efficiency: Reduced friction leads to better energy efficiency and lower operational costs.
- Improved Performance in Harsh Environments: Herringbone gears are ideal for applications requiring extreme precision and durability.
Applications of High Precision Herringbone Gear
High precision herringbone gears are widely used across various industries, including:
- Aerospace: Used in aircraft engines and transmission systems.
- Automotive: Found in heavy-duty trucks and high-performance vehicles.
- Oil & Gas: Critical components in drilling rigs and pipeline compressors.
- Marine: Essential for ship propulsion and power transmission.
- Power Generation: Used in turbines, wind energy systems, and hydroelectric plants.
Conclusion
Herringbone gears play a vital role in industrial applications requiring high strength, precision, and durability. The high precision industrial herringbone gear manufacturing process involves meticulous material selection, precise machining, rigorous heat treatment, and thorough quality control to produce gears that meet the highest standards. With ongoing advancements in manufacturing technology, the future of herringbone gear production promises even greater efficiency, reliability, and performance.
Whether in aerospace, automotive, or heavy machinery, the importance of high-quality herringbone gears cannot be overstated. By investing in precision manufacturing, industries can achieve superior mechanical performance, reduced downtime, and long-term cost savings. If you're looking for the best in gear technology, high precision herringbone gears are undoubtedly a top choice.
https://www.lrfgears.com/High-Precision-Industrial-Herringbone-Gear-Manufacturing.html
www.lrfgears.com
Longruifa