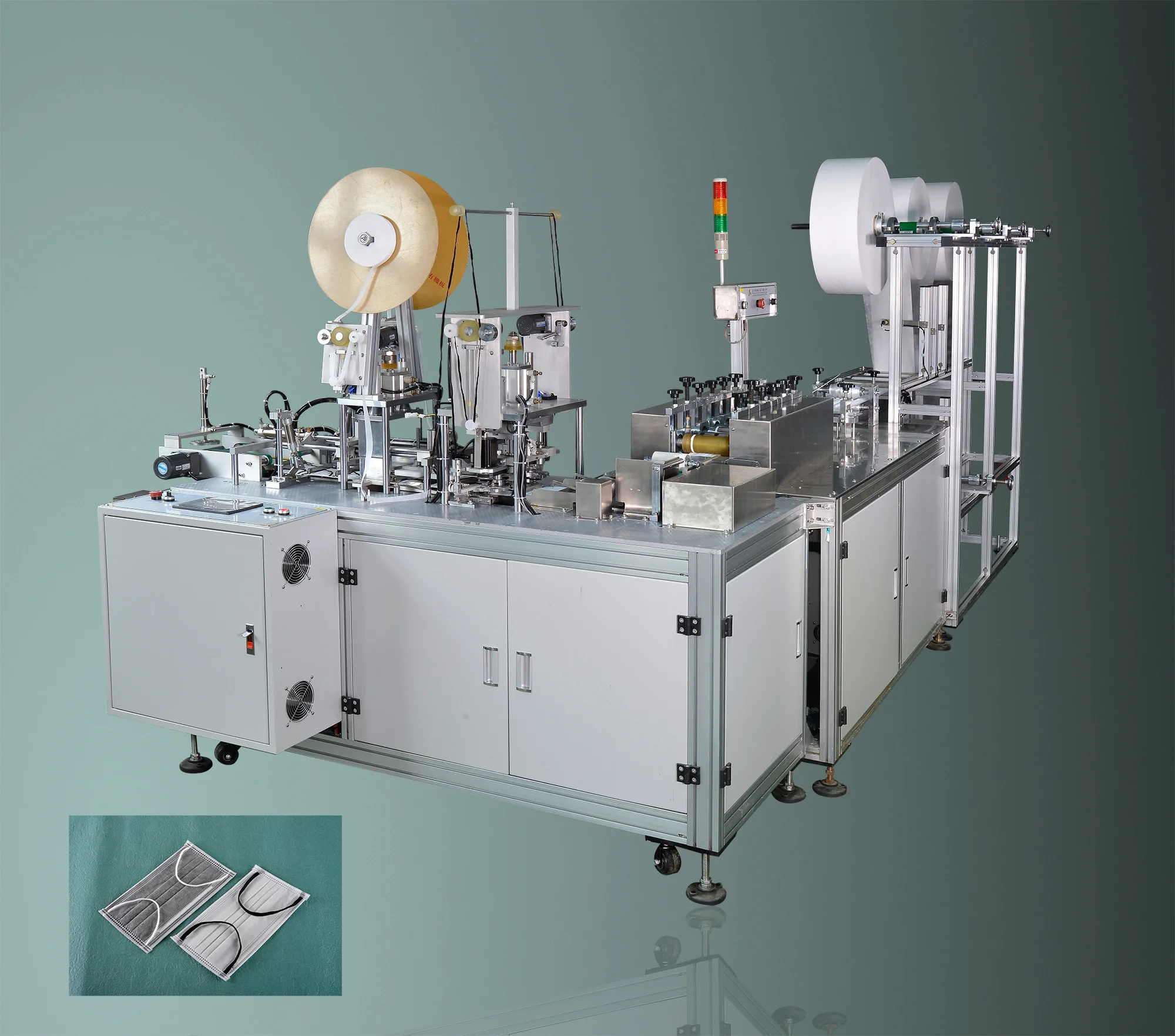
In today's world, the importance of personal protective equipment (PPE) has become increasingly evident across various sectors. At the forefront of this demand is the full automatic face mask making machine, a technological marvel that streamlines the production of face masks with remarkable efficiency and precision. These advanced machines automate every stage of the manufacturing process, from material feeding to final packaging, ensuring consistent quality and high output. As industries seek reliable solutions to enhance safety and protect individuals, understanding the role of these automated systems becomes crucial in shaping the future of mask production and personal safety standards. This article explores the technology behind these machines, their operational processes, and their significant impact on manufacturing practices.
Understanding Full Automatic Face Mask Making Machines
Full automatic face mask making machines are advanced production systems designed to manufacture face masks with minimal human intervention. These machines automate the entire process of mask production, from material feeding to packaging, ensuring high efficiency and consistent quality.
Key Components of Automatic Face Mask Making Machines
Material Feeding System: This component feeds raw materials into the machine, typically including non-woven fabrics like polypropylene, which are essential for mask production.
Mask Body Formation: The machine cuts and shapes the fabric into mask bodies. This process often includes folding and welding the layers together using ultrasonic technology.
Nose Wire Insertion: A mechanism is integrated to insert a nose wire into the mask, which helps create a snug fit around the wearer’s nose.
Ear Loop Welding: Ear loops are attached to the sides of the mask through ultrasonic welding, ensuring durability and comfort.
Quality Control Systems: Many machines incorporate sensors and cameras to monitor production quality in real-time, ensuring that only masks meeting specified standards proceed to packaging.
Packaging System: Finished masks are automatically packaged into boxes or bags for distribution, completing the production cycle.
The Production Process
The operation of a full automatic face mask making machine can be broken down into several key stages:
1. Material Preparation
The process begins with unwinding rolls of non-woven fabric from their spools. The fabric is typically composed of three layers: an outer layer made from spunbond polypropylene, a middle layer of meltblown polypropylene for filtration, and an inner layer that is also spunbond polypropylene for comfort against the skin.
2. Mask Body Formation
Once the materials are fed into the machine, they are cut into pre-defined dimensions. The machine then folds and welds these layers together using ultrasonic technology, creating a sealed mask body without the need for adhesives or sewing.
3. Inserting Nose Wire
During this stage, a flexible metal strip is inserted into the top edge of the mask. This wire allows users to mold the mask around their nose for a better fit, which is crucial for effective filtration and comfort.
4. Attaching Ear Loops
Next, ear loops are attached to both sides of the mask using ultrasonic welding techniques. This method provides a strong bond while maintaining the integrity of the mask material.
5. Quality Assurance
As masks are produced, integrated quality control systems continuously monitor for defects such as misalignment or incomplete welds. Any defective masks are automatically rejected from the production line.
6. Packaging
Finally, completed masks are automatically packaged for shipment. This step may include labeling and boxing based on customer specifications.
Advantages of Full Automatic Face Mask Making Machines
The adoption of full automatic face mask making machines offers numerous advantages over traditional manufacturing methods:
1. High Production Capacity
These machines can produce between 100 to 200 masks per minute, significantly increasing output compared to manual methods or semi-automatic systems. This high capacity is essential in meeting urgent demands during public health crises.
2. Consistent Quality
Automation ensures that each mask produced meets stringent quality standards with minimal variability. The precision of automated systems reduces human error and enhances product reliability.
3. Reduced Labor Costs
By minimizing human intervention in the production process, companies can significantly reduce labor costs associated with manual assembly lines while reallocating human resources to other critical areas.
4. Flexibility and Customization
Many modern machines offer customizable settings that allow manufacturers to produce different types of masks (e.g., surgical masks, N95 respirators) by simply adjusting parameters rather than requiring entirely new setups.
Applications Beyond Medical Use
While primarily desigar, manufacturers can use these machines to create fashionable masks that meet both safety standards and aesthetic preferences.
3. Emergency Preparedness
Organizations focused on disaster relief or emergency response can benefit from the on-demand production capabilities these machines offer, allowing them to quickly produce necessary PPE during a crisis.
Conclusion
The development of fully automatic mask manufacturing machines represents a major advancement in PPE manufacturing technology. By automating every aspect of mask production, from material feeding to packaging, these machines provide unparalleled efficiency, consistency, and adaptability in meeting global health needs. With their high production output and quality assurance capabilities, fully automatic mask manufacturing machines will undoubtedly play a key role in shaping the production of personal protective equipment.
Streamlining Face Mask Production with the Full Automatic Face Mask Making Machine
www.broadfairmachine.com
Broadfair Automation Equipment Co., Ltd.