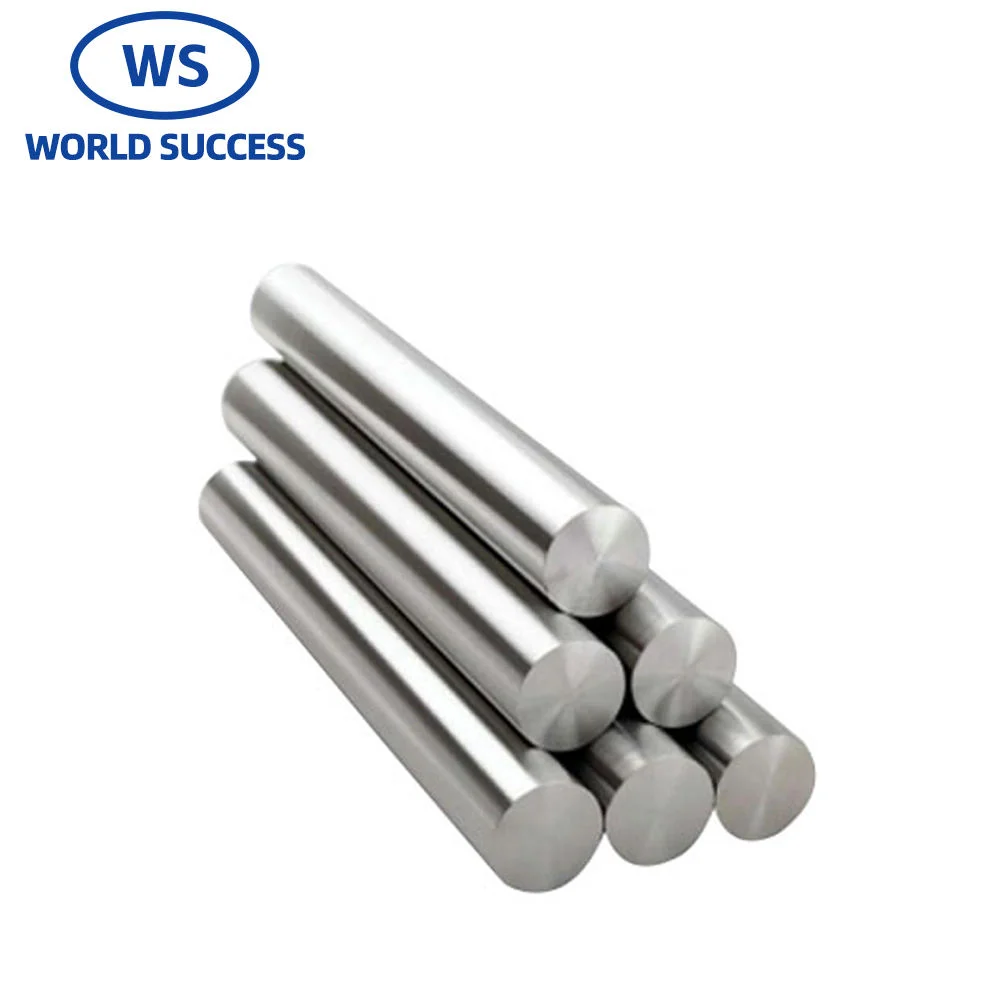
Induction hardening is a heat treatment process that offers numerous advantages for pin shafts. This article explores the benefits of induction hardening and its impact on the performance and durability of pin shafts.
Understanding Induction Hardening
Induction hardening is a surface hardening technique that involves heating the surface of a pin shaft using high-frequency induction heating. The localized heating is followed by rapid quenching, resulting in a hardened surface layer with a tough and ductile core.
Enhanced Wear Resistance
One of the primary benefits of induction hardening for pin shafts is the significant improvement in wear resistance. The hardened surface layer forms a protective barrier against abrasion, reducing the wear and tear caused by friction and contact with other components. This leads to increased longevity and reduced maintenance costs.
Increased Strength
Induction hardening enhances the strength of pin shafts, making them more resistant to bending, torsion, and other mechanical stresses. The hardened surface layer improves the overall load-bearing capacity of the pin shaft, allowing it to withstand higher loads without deformation or failure. This increased strength contributes to the overall reliability and performance of the pin shaft.
Improved Fatigue Resistance
Pin shafts often experience cyclic loading, leading to fatigue failure over time. Induction hardening significantly improves the fatigue resistance of pin shafts by creating a hardened surface layer that can withstand repeated stress cycles without cracking or breaking. This ensures the pin shaft can endure prolonged usage without compromising its structural integrity.
Precise Hardening Control
Induction hardening offers precise control over the hardening depth and pattern, allowing manufacturers to tailor the process according to specific design requirements. This flexibility ensures that the hardened layer is precisely localized to the areas that require enhanced strength and wear resistance, while maintaining the desired core properties.
Cost-Effective Solution
Compared to other surface hardening methods, induction hardening is a cost-effective solution for pin shafts. The localized heating reduces energy consumption, while the rapid quenching minimizes distortion and warping. Additionally, the improved wear resistance and strength of induction-hardened pin shafts result in longer service life, reducing the need for frequent replacements and maintenance.
Conclusion
Induction hardening offers numerous benefits for pin shafts, including enhanced wear resistance, increased strength, improved fatigue resistance, precise hardening control, and cost-effectiveness. By incorporating induction hardening into the manufacturing process, pin shafts can achieve superior performance, durability, and reliability in various applications.
Differential and Axle: Key Components for Power Transmission in Vehicles
www.zjg-ws.com
Worldsuccess Machinery