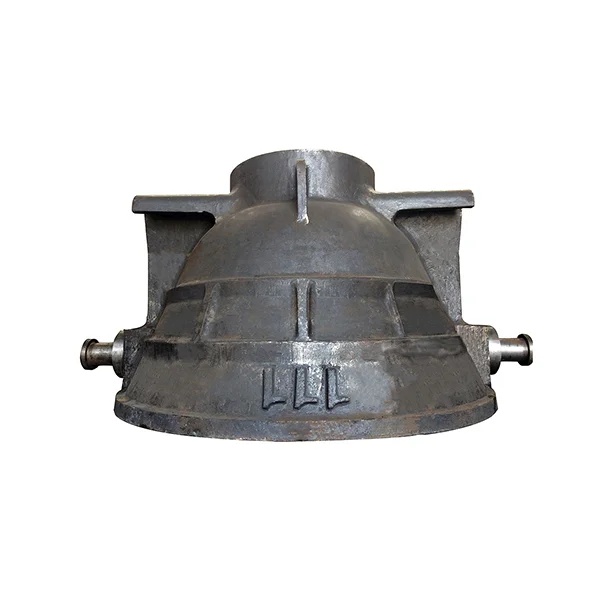
Metal rolling mills are complex and highly demanding machines, and their efficient operation depends on the longevity of each component. The parts in a rolling mill are subjected to extreme pressures, temperatures, and continuous wear, making proper maintenance critical to ensuring their optimal performance and extending their lifespan. In this article, we’ll explore essential maintenance tips for the different parts of metal rolling mills and how proactive care can help avoid costly repairs and unplanned downtime.
1. Rolls: The Heart of the Rolling Mill
Rolls are the most critical component in a metal rolling mill, as they are responsible for shaping and reducing the metal’s thickness. Since rolls are exposed to constant pressure, friction, and thermal cycles, it’s essential to maintain them properly.
Maintenance Tips for Rolls:
· Regular Inspection: Inspect the rolls for signs of wear such as cracks, surface damage, or pitting. Early detection of these issues can prevent more significant damage.
· Check for Misalignment: Misaligned rolls can cause uneven pressure distribution, leading to product defects. Ensure proper alignment and adjust as needed.
· Surface Cleaning: Clean the roll surfaces regularly to remove metal dust, slag, and other contaminants that could cause abrasion or corrosion.
· Correct Lubrication: Apply high-quality lubricants to reduce friction and wear on the rolls. Regularly check for any lubrication system malfunctions to ensure continuous lubrication.
2. Bearings: Keeping Everything in Motion
Bearings support the weight and allow the rotation of rolls, reducing friction and ensuring smooth operation. Bearings are subject to heavy loads and high-speed rotations, making them prone to wear and failure if not maintained properly.
Maintenance Tips for Bearings:
· Monitor Vibration: Excessive vibrations can indicate misalignment or worn bearings. Use vibration monitoring tools to track performance and detect early signs of damage.
· Temperature Checks: Overheating can lead to premature failure of bearings. Ensure that the temperature remains within the manufacturer’s specified range. Install temperature sensors if necessary.
· Lubrication: Bearings require constant lubrication to operate efficiently. Keep an eye on oil levels and check for contamination. Re-lubricate them regularly according to the manufacturer’s recommendations.
· Replacement Schedule: Even with proper maintenance, bearings will eventually wear out. Establish a replacement schedule based on operating hours and performance data to avoid unexpected breakdowns.
3. Gearbox: Power Transmission and Reliability
The gearbox transmits power from the motor to the rolls, converting motor torque to the necessary rolling force. Since gearboxes are subject to high-stress levels, their maintenance is crucial for maintaining the performance of the entire system.
Maintenance Tips for Gearboxes:
· Inspect Gear Teeth: Periodically inspect the gear teeth for signs of wear, cracks, or chips. Damaged teeth can lead to further complications in the gearbox and should be replaced immediately.
· Lubrication: Use the correct grade of lubricant and ensure that oil levels are maintained. Dirty or low lubricant levels can cause the gearbox to overheat and fail prematurely.
· Monitor Noise Levels: Unusual sounds, such as grinding or whirring, can be signs of gear misalignment or wear. Investigate immediately to prevent further damage.
· Check for Leaks: Ensure that seals are intact and that no oil leaks occur, which could affect the performance and longevity of the gearbox.
4. Hydraulics: Ensuring Precision and Consistency
Hydraulic systems are responsible for adjusting the roll gap and controlling the pressure during the rolling process. Given their crucial role in maintaining precise control, hydraulic components require regular maintenance to ensure consistent performance.
Maintenance Tips for Hydraulics:
· Inspect Hydraulic Fluid: Regularly check the hydraulic fluid levels and quality. Contaminated fluid can cause corrosion and damage to components. Always replace fluids as per the manufacturer’s guidelines.
· Check for Leaks: Hydraulic leaks are a common issue that can significantly affect system efficiency. Inspect hoses, fittings, and seals for any signs of leakage.
· Clean Filters: Hydraulic filters prevent contaminants from entering the system and causing damage. Clean or replace filters regularly to maintain system cleanliness.
· Monitor Pressure: Ensure that the pressure settings are correct and that the system operates within the recommended pressure ranges. Inconsistent pressure can lead to poor control and equipment malfunction.
5. Cooling and Lubrication Systems: Preventing Overheating and Wear
Cooling and lubrication systems are essential to maintaining the temperature and reducing friction in the rolling mill. If these systems are not functioning properly, components can overheat or wear out prematurely.
Maintenance Tips for Cooling and Lubrication Systems:
· Inspect Coolant Levels: Regularly check the coolant levels and ensure that there are no blockages in the cooling lines. If coolant is low or contaminated, replace it immediately.
· Clean Radiators and Heat Exchangers: Dust and debris can clog cooling systems, reducing efficiency. Regularly clean radiators, heat exchangers, and cooling fans to maintain proper airflow and cooling performance.
· Lubrication Quality: Ensure that lubrication systems are providing clean, high-quality oil to critical components such as bearings, rolls, and gears. Check for contamination or degradation of lubricant and replace it as needed.
· Automated Lubrication: Consider installing an automated lubrication system to provide consistent and precise lubrication to high-wear areas.
6. Electrical and Control Systems: Monitoring Performance
Modern rolling mills are equipped with advanced electrical and control systems that help monitor and regulate various components, including speed, pressure, and temperature. Proper maintenance of these systems is essential for ensuring efficient operation.
Maintenance Tips for Electrical and Control Systems:
· Regular Calibration: Ensure that sensors and control systems are calibrated to provide accurate readings. Miscalibration can lead to improper adjustments and increased wear on components.
· Check for Faults: Regularly perform diagnostic checks to identify any electrical faults or issues in the control panels, wiring, or sensors.
· Maintain Cleanliness: Dust, dirt, and moisture can damage electrical systems. Keep control panels and electrical components clean and dry to avoid short circuits or electrical failures.
· Update Software and Firmware: For mills with computerized control systems, ensure that software and firmware are up-to-date to avoid glitches and improve performance.
7. General Maintenance: Keep the Mill in Optimal Condition
In addition to focusing on individual components, regular general maintenance is necessary to keep the entire rolling mill running smoothly.
General Maintenance Tips:
· Create a Maintenance Schedule: Set up a regular maintenance schedule to track and manage all maintenance activities, ensuring nothing is overlooked.
· Preventative Maintenance: Don’t wait for parts to fail. Regular inspections and replacing worn-out components before they fail will save time and money in the long run.
· Training for Operators: Ensure that operators are well-trained in recognizing early signs of wear and malfunction, as they are often the first to notice problems during operation.
Conclusion
Metal rolling mills are vital for the production of high-quality metal products, and ensuring the longevity of their components is essential for maintaining efficiency and reducing downtime. By regularly inspecting and maintaining key parts such as rolls, bearings, gearboxes, hydraulic systems, and cooling systems, you can extend the lifespan of your equipment and keep your mill running smoothly.
www.swasps.com
Jiangsu Sawei Equipment Technology Co., Ltd.