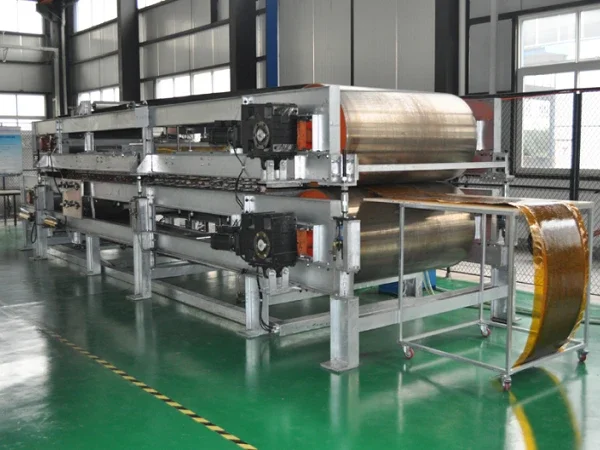
In industrial manufacturing, granulation is a crucial process that converts powdery materials into solid, stable granules for easier handling, transportation, and further processing. From chemicals and fertilizers to food products and plastics, granulation plays an essential role in a wide range of industries. One indispensable piece of equipment in the granulation process is the belt cooler.A belt cooler is a cooling system designed to solidify granulated materials by efficiently reducing their temperature. It plays a pivotal role in the granulation process, ensuring that hot, freshly formed granules cool down to maintain their shape, structure, and overall quality. This article Little Sky delves into the critical role of belt coolers in granulation.
The Critical Role of Belt Coolers in Granulation Processes
Granulation involves converting powdery materials into solid granules through mechanical, thermal, or chemical processes. Typically, the granules are formed at high temperatures, often in molten or semi-molten states, requiring rapid cooling to maintain their shape and structure. Belt coolers are integral to this cooling phase, ensuring that granules are stabilized and properly solidified without deformation or sticking together.
Preventing Granule Deformation and Quality Degradation
One of the primary roles of belt coolers is to ensure that freshly produced granules maintain their intended shape and structural integrity. Hot granules, if not cooled efficiently, are prone to deformation. This can result in clumping or a loss of uniformity, which adversely impacts product quality. Belt coolers provide controlled, uniform cooling, reducing the chances of such deformities and ensuring that the granules meet the required specifications.
Quality degradation is another concern. Granules must often adhere to strict quality parameters, such as size, porosity, hardness, and moisture content. Effective cooling using belt coolers ensures that these characteristics are preserved, resulting in higher-quality end products. For example, in the polymer industry, improper cooling can lead to inconsistent pellet sizes, affecting downstream processing like injection molding.
Ensuring Process Efficiency and Throughput
Belt coolers are designed for continuous operation, which significantly enhances production efficiency. Unlike batch cooling methods, which require time-consuming loading and unloading, belt coolers offer a seamless flow of materials through the cooling process. This continuous operation is particularly advantageous for large-scale production environments, as it minimizes downtime and maximizes throughput.
Additionally, the ability to control the cooling rate allows operators to optimize the process for different materials, ensuring that the granules are cooled at the ideal speed to prevent defects while maintaining a high production output. This precise control over cooling conditions is a significant factor in ensuring that products are manufactured consistently and efficiently.
Safety in Handling and Storage
When granules emerge from the granulation process at high temperatures, they pose significant safety risks in terms of handling, packaging, and storage. For instance, if granules remain excessively hot, they could damage packaging materials or cause burns and other injuries to workers. In extreme cases, hot granules can even pose fire hazards or lead to the ignition of flammable materials.
Belt coolers play a crucial role in mitigating these risks by rapidly cooling granules to a safe temperature for handling and storage. This ensures that the materials can be safely packaged without risk of damage or safety incidents. For example, in fertilizer manufacturing, where granules are typically stored in bulk, belt coolers ensure the granules are cool enough to prevent spontaneous combustion or other hazardous reactions.
The Advantages of Belt Coolers Over Other Cooling Methods
While several cooling methods are available for granulated materials, belt coolers offer distinct advantages that make them the preferred choice in many industrial applications. These advantages stem from their continuous operation, customizable cooling capabilities, and ability to handle a wide range of materials.
Continuous Cooling for High-Throughput Production
One of the main benefits of belt coolers is their ability to operate continuously, making them ideal for high-volume production environments. Unlike batch cooling systems, which require periodic stops and starts, belt coolers provide a steady, uninterrupted flow of materials through the cooling process. This continuous operation helps increase throughput and reduce production downtime, leading to higher overall efficiency.
For manufacturers handling large quantities of granules daily, such as in the plastics or chemical industries, this uninterrupted cooling process is invaluable. It not only speeds up production but also ensures that the cooling process is consistent, leading to uniform product quality across large production runs.
Gentle Handling to Prevent Damage
Belt coolers offer gentle handling of materials, which is particularly important for fragile or sensitive products. Unlike other cooling methods that may involve harsh mechanical action, such as tumbling or spraying, belt coolers transport granules on a smooth, flat surface. This reduces the risk of damage, such as chipping, cracking, or deformation, especially for products that require precise shapes and sizes.
For example, in the food industry, granules like instant coffee, snack pellets, or granulated sugar must retain their structural integrity during cooling. Belt coolers ensure that these products are handled delicately, preserving their texture and appearance while preventing damage that could affect product quality or consumer satisfaction.
Customizable Cooling for Precise Control
Belt coolers offer unparalleled control over the cooling process, allowing manufacturers to adjust various parameters to achieve the desired results. By controlling the speed of the conveyor belt, the intensity of the airflow, and the temperature within the cooling zones, operators can tailor the cooling process to the specific needs of each material.
This level of customization is particularly beneficial in industries where product specifications are critical. For example, in the pharmaceutical industry, granules may need to be cooled at a specific rate to ensure that active ingredients remain stable and effective. Belt coolers provide the precise control needed to meet these stringent requirements, ensuring that the final product meets the necessary standards for safety, efficacy, and quality.
Belt coolers are essential tools in the granulation processes of various industries, providing efficient, controlled, and uniform cooling of granulated materials. From chemicals and polymers to food products and pharmaceuticals, belt coolers play a critical role in ensuring the quality and safety of the final product.Their continuous operation, gentle handling, and customizable cooling rates make them the preferred choice for many manufacturers. By providing precise control over the cooling process, belt coolers help to achieve consistent results, minimize waste, and reduce energy consumption.
https://www.th-littlesky.com/Double-Belt-Laminating-Machine
www.th-littlesky.com
Little Sky Mechanical Engineering Thailand Co.,Ltd